A fiber six times stronger than steel
Aramid, short for "aromatic polyamide," is a class of synthetic, high-performance fibers. Meta-aramid fibers were first commercially applied in the early 1960s, with para-aramid fibers being developed in following decade. They are unique because their structures, characterized by polymer chains, are linked through powerful hydrogen bonds that efficiently transfer mechanical stress.
These characteristics make aramids perfectly suited to various industries like automotive, aerospace and defense, where heat resistance and exceptional strength are vital.

What is an aramid?
Aramids are man-made fibers with enhanced structural properties, known for their incredible tensile strength. They are used in advanced products where light weight, yet high strength is needed.
Aramid fibers are made from long-chain synthetic polyamides. The chemical composition of para-aramid is poly para-phenyleneterephthalamide (PPTA). This polymer is composed of alternating benzene ring and amide groups, leading to a rigid, rod-like structure.
Characteristics of aramid fibers
Aramids fibers show resistance to many solvents and salt, but can be weakened by strong acids. While they are difficult to dye and sensitive to UV light, they are hard to burn, and instead of melting, they decompose.
Aramid products are available as filament yarn, staple fiber or pulp. They retain much of their strength at high temperatures and resist permanent deformation or 'creep' under prolonged stress. Their toughness surpasses steel, glass fiber and nylon, and they show high durability even under extreme tension and bending, making them incredibly versatile.
Meta-aramid vs para-aramid
The difference between meta- and para-aramids lies in the alignment of their chemical bonds. Para-aramids have bonds that run along the length of the fiber, contributing to their high tensile strength. Meta-aramids have bonds arranged in a zigzag pattern, resulting in a lower tensile strength compared to para-aramids.

The all-round high performer. Suitable for manufacturers of products that need to be stronger, lighter, and more resistant to chemicals.

The premium para-aramid. It’s six times as strong as steel, with great heat and chemical resistance, ideal for industrial and reinforcement applications.

High-performance protection. This meta-aramid offers excellent resistance to heat, flame and chemicals, making it ideal for use in the manufacture of protective textiles and other industrial applications.
Properties of Twaron®, Technora® and Teijinconex®
We manufacture high-performance aramid materials under distinct brand names. These include Twaron® and Technora®, para-aramids produced in Emmen and Japan respectively. Meta-aramid Teijinconex® is produced in our facilities in Japan and Thailand.
Property | Meta-aramid (Teijinconex®) | Para-aramid (Twaron® & Technora ®) |
---|---|---|
Mechanical properties | Easy to process, soft and flexible. | Exceptional tensile strength, 2 – 3 times stronger than polyester and up to 6 times stronger than steel. |
Dimensional stability | Provides abrasion resistance in protective clothing. | Shows minimal deformation or shrinkage under a wide range of conditions. |
Thermal properties | Heat resistant up to 250°C (482°F) and is inherently flameproof. | Twaron® and Technora® are heat resistant up to 190°C (374°F) and 210°C (410°F) respectively. Both demonstrate excellent thermal stability and low heat conductivity. |
Chemical resistance | Excellent resistance to chemical degradation. | High resistance to organic chemicals. |
Other properties | Provides a longer lifetime for products that operate in severe heat conditions: firefighter gear, industrial worker PPE, and racing driver apparel. | Provides a long economic lifetime for the end product. Technically well-established flagship product. |
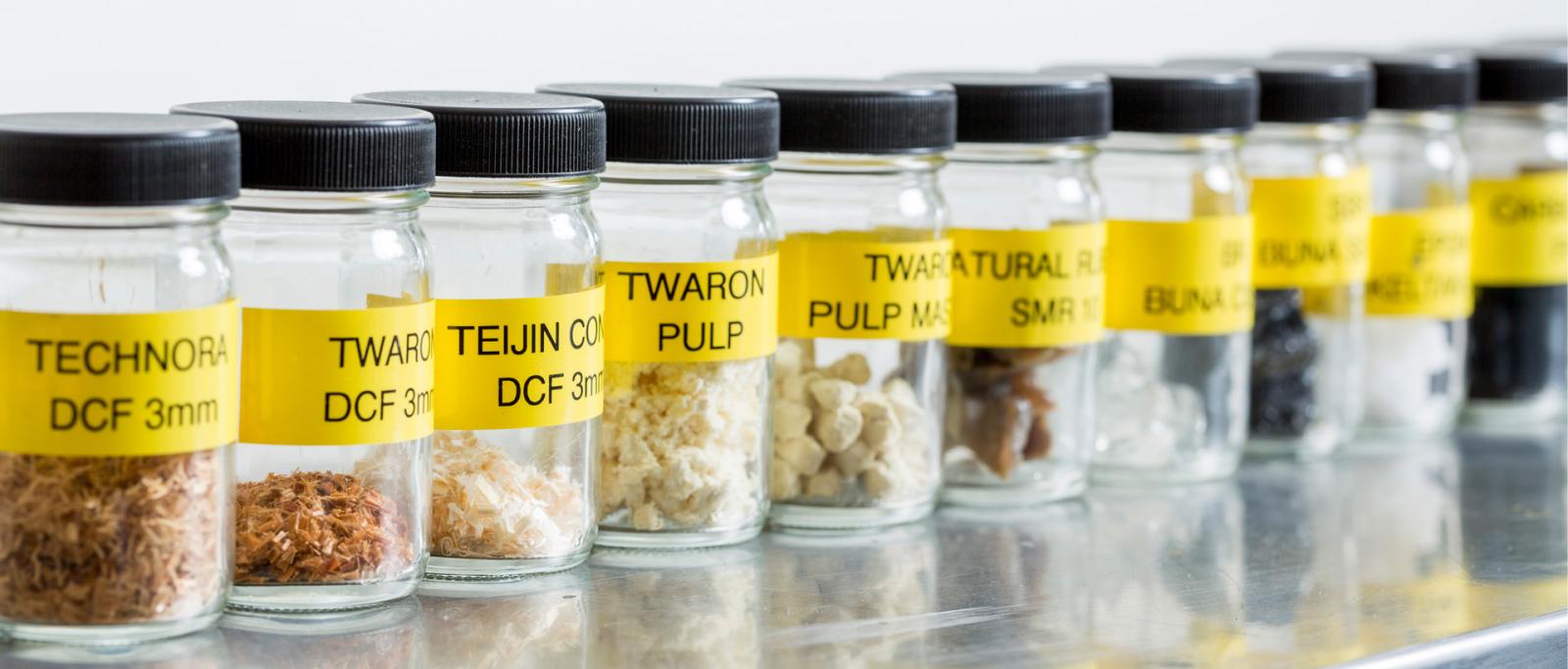
Production process of the para-aramid Twaron®
Around the world, all our global site operations are underpinned by a rigorous system that ensures compliance with relevant laws and regulations. As such, our operations meet high quality, health and environmental standards. Our materials also meet the highest regulatory standards.
Dedicated specialists in our manufacturing departments continually monitor the production of Twaron®, which is made from monomers in several stages: polymerization, continuous filament yarn spinning and converting.
Step 1: Polymerization
The process begins with the combination of monomers to form a sturdy, finely-grained para-aramid polymer. This material has the typical heat resistance and chemical properties of para-aramid.
Step 2: Continuous filament yarn spinning
Next, the polymer is dissolved in sulfuric acid to create a liquid crystalline solution. The solution is then spun into fine, naturally yellow or dye-infused continuous filament yarns by a wet-spinning process. These fibers are completely crystalline, with molecular chains running parallel to the filament axis, providing the yarns with their unique properties.
Step 3: Converting
In the final stage, the continuous filament yarns are crimped to produce staple fiber, treated with a finishing agent, and then cut to the desired length to create short-cut fibers. The untwisted continuous filament yarns can now also be twisted to enhance their fit-for-use characteristics.
Step 4: Converting to pulp
Filament yarns are chopped and mixed with water to form a fibrous substance called wet pulp. This wet pulp can be sold directly or dried to create and sell as dry pulp.

Industries
Applications where aramids are used
Thanks to their high strength, heat resistance and lightweight properties, aramid fibers have made a major impact across a wide range of industries.